Case Studies
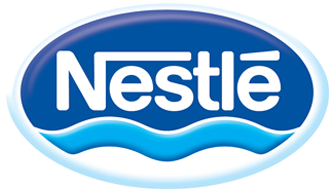
All UK Production sites 2021 & 2022
In-order to comply with the HSE CEMFAW Regs 2016, Nestle UK Ltd commissioned Scholes EMF to undertake EMF Assessments at each of their 8 x UK manufacturing sites following an earlier & successful EMF Assessment at their Buxton Water site in 2017. These were typical CEMFAW Regs compliance EMF Assessments for a fairly “low-risk” industry (Food & Drinks) in EMF terms ie) equipment requiring Assessments / measurements were for example Welding, Transformers, Substations, Switchrooms, in-line Magnets (not good news for anyone with an electronic implant!), exposed Motors & Pumps, FLT Chargers, Workshop Equipment etc. Nestle chose Scholes EMF Ltd based on their earlier experience with us at Nestle Buxton Water site, and particularly because of the easy-to-understand and comprehensive Report.
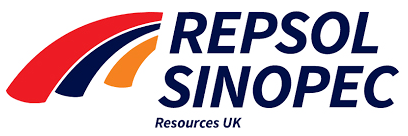
3 x North Sea Oil Rigs 2020
A very unusual & fascinating EMF Assessment project, as well exciting as it meant a Helicopter ride out from Aberdeen Airport to each of the Oil Rigs (…though definitely not as glamorous as it sounds as it turned out!). Unfortunately the EMF Meters had to go by boat in the choppy North Sea a couple of weeks before as they can’t be carried on-board a Helicopter…. a nail-biting time considering their combined value of something like £10,000, but luckily they arrived safe & sound if a little sea-sick. I soon realised however that Oil Rigs are simply “floating factories” and in fact fairly low-risk in EMF-terms despite their size & complexity, and each one took about 2-days to complete fully. Again, EMF Assessments were required for compliance with the UK HSE CEMFAW Regs 2016 and the client was very happy with the easy-to-read Reports written for each Platform. They also very much appreciated Scholes EMF Ltd affixing the EMF warning stickers onto equipment / areas where required as part of the Assessments as it saved then having to do it afterwards.

Brimsdown site 2021
Again for CEMFAW Regs compliance, but more complex and high-risk in EMF terms as the site had a number of Induction Furnaces which have notoriously high EMFs – Induction heating (as opposed to gas or electrical heating) requires huge electrical currents to quickly & efficiently heat-up to >1200 degrees in-order to melt metals such as steel, iron etc. Johnson Matthey were very pleased with Assessment & Report, particularly as it contained the relevant Actions required to comply with the Regs despite the Action Levels being (inevitably) exceeded at the Furnaces. They also appreciated the Actions required, and the measured “safe” distances, in-terms of anyone “at particular risk” to EMFs eg) those wearing electronic implants in-relation to the Induction Furnaces – basically prohibit entry to the Furnace plant…!